Motivation
Among the typical failure scenarios of bolted joints, the self-loosening plays a significant role. During the self-loosening process, the joint friction can be overcome due to relative displacements, which causes a partially or completely drop of the pre-tension. That leads to a functional loss of the bolted connection and is usually associated with severe damage. A design concept ensuring the reliability of the bolted joints against loosening is not provided in any current standard or guidelines. However, a proper investigation of the self-loosening and an evaluation of its risks at an early stage of the design process would help to prevent damage and the related costs.
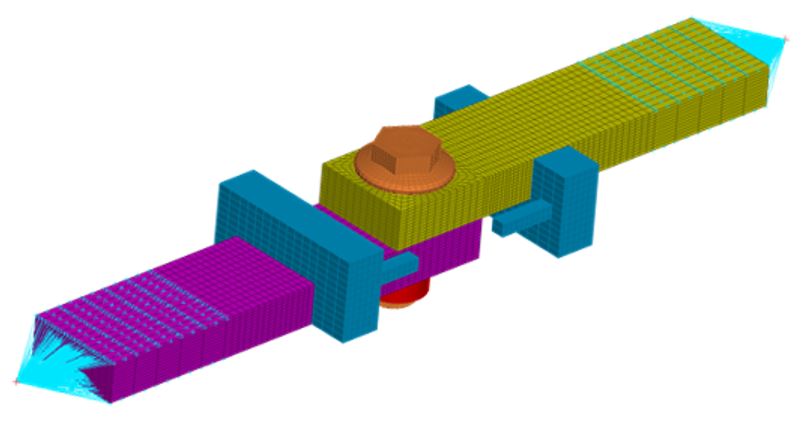
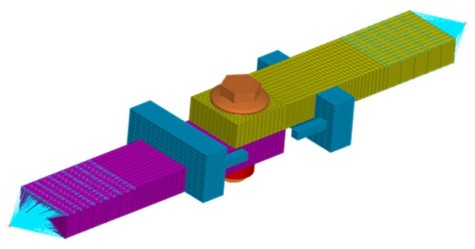
Objective
The aim of the project is the development of both, a modelling method to represent the non-linear force-displacement behavior of bolted joints subjected to a transverse force and an approach to analyze the self-loosening behavior of bolted connections by means of experimentally and numerically determined relative displacements.
Solution
The bolts are first examined on a tightening test rig to determine the friction coefficients. The experimental results in terms of limit curves (relative displacement over the number of cycles) provide a correlation between the number of cycles for loosening and the significant influence variables (friction, preload, clamping length, load magnitude). By means of the Finite-Element analysis, the relative displacements in the bolted joint are numerically investigated and the influence of various modeling approaches is analyzed. For this purpose, complex 3D models are generated first and the influence of different contact algorithms and friction definitions on the relative displacement processes is examined. The validation of the numerical modeling is based on a strain analysis. In addition, simplified numerical models with shell and bushing elements are generated on the basis of numerical results from the complex model.
Information about the project
Research facilities:
- Technical University Darmstadt, State Material Testing Lab Darmstadt (MPA) and the Institute for Material Science (IfW)
- Technical University Darmstadt, Research group System Reliability, Adaptive Structures, and Machine Acoustics (SAM)
AVIF-Project
Research Association for Automotive Technology FAT e.V.
Duration: 24 months
Contact
M.Sc. Elena De Tomaso
Tel: +49 6151 705 8458
Email: elena.de.tomaso@sam.tu-darmstadt.de