Slender beam-columns in lightweight mechanical load-bearing structures are sensitive to failure by buckling when loaded by compressive axial loads. The maximum bearable axial load of a beam-column is considerably reduced by uncertainty in the material, geometry, loading or support properties, but may be increased by active buckling control. In the subproject C2 of the Collaborative Research Center 805, active buckling control of a practical beam-column system with circular cross-section, relatively low slenderness ratio and relatively high critical buckling load as well as dynamic axial loads is investigated (shown in figure 1).
The goal is to increase the maximum bearable axial load and reduce uncertainty in the buckling behavior. For the latter, probabilistic uncertainty in the maximum bearable axial loads and lateral deflections of the passive and active beam-column systems is quantified and evaluated experimentally. For the experimental results under quasi-static axial loads (shown in figure 2), the most likely maximum bearable axial load increases by 29% and the variability reduces by 70% when comparing the passive beam-column system. Overall, the results of this subproject contribute to the application of active buckling control in practical truss structures.
In current research, active buckling control of three-dimensional truss structures is investigated (shown in figure 3). Quasi-static and dynamic performance of the passive and active truss structures against axial load will be compared. Furthermore, the uncertainty of buckling control of the truss structures under axial dynamic load will be quantified and evaluated.
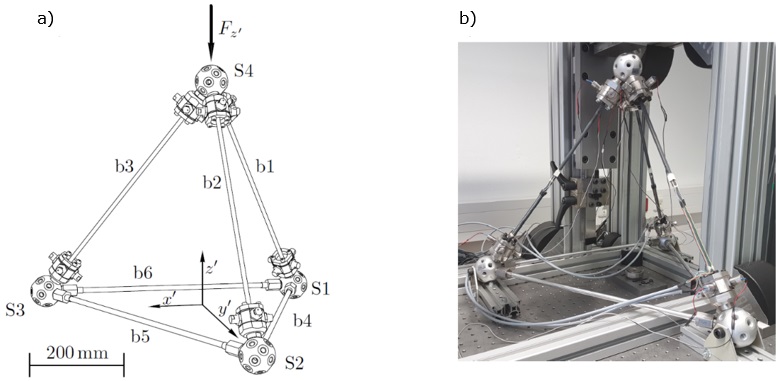
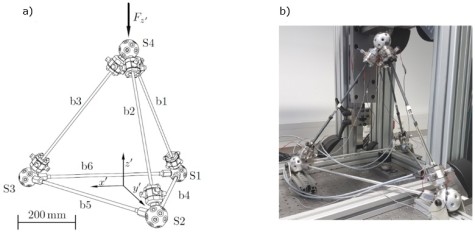
Contact: Dr.-Ing. Maximilian Schäffner